E-TAC water splitting technology improves the energy efficiency of the process of producing hydrogen from water to an unprecedented record of 98.7%, and significantly reduces carbon dioxide emissions. The startup company H2Pro based on the development will translate it into a commercial application
Technion researchers have developed a technology
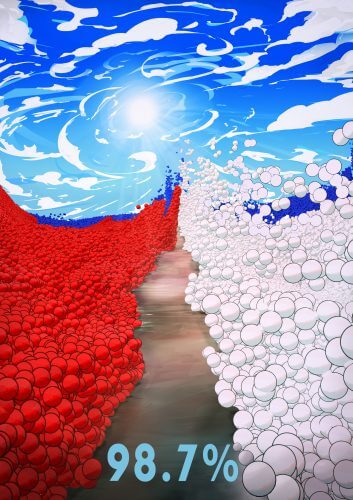
Clean, cheap and safe for hydrogen production. The technology significantly improves the efficiency of hydrogen production - from about 75% in today's accepted methods to an unprecedented energy efficiency of 98.7%. The research was conducted within the Nancy and Stephen Grand Technion Energy Program (GTEP) by Prof. Avner Rothschild from the Faculty of Materials Science and Engineering and Prof. Gideon Gerder from the Faculty of Chemical Engineering together with Dr. Chen Dotan and PhD student Abigail Landman. The results of the study were published in the journal Nature Energy.
Electrolysis was discovered over 200 years ago, and since then has undergone a cumulative collection of spot improvements. Now the Technion researchers present a dramatic change that will lead to their assessment of cheap, clean and very safe hydrogen production. According to them, the new process may revolutionize hydrogen production, while being based on clean and renewable energy such as solar energy or wind energy.
The researchers developed an innovative and unique process, E-TAC water splitting (Electrochemical - Thermally-Activated Chemical water splitting), based on a cyclic operation, in which the chemical composition of the anode (the electrode where the oxidation process takes place in the system) alternately changes. In the first stage, the cathode (the electrode where the redox process takes place in the system) produces hydrogen and the anode changes the chemical composition without producing oxygen; In the second stage the cathode is passive while the anode produces oxygen. At the end of the second stage, the anode returns to its initial position and the cycle begins again. Based on this technology, the researchers founded the startup company H2Pro, which deals with its translation into a commercial application.
Worldwide, huge amounts of hydrogen are produced every year: about 65 million tons worth about 130 billion dollars, which are energetically equivalent to about 9 exa-joules (EJ) which are about 2,600 terawatt-hours (TWh). These amounts are growing steadily and are expected to triple in the next 20 years; In 2030, hydrogen consumption is expected to stand at 14 exa-joules and in 2040 at 28.
About 53% of the hydrogen produced today is used in the production of ammonia for fertilizers and other materials, 20% is used in refineries, 7% in the production of methanol and 20% in other uses. In the future, hydrogen is expected to be used in additional applications, some of which are in accelerated development stages: hydrogen as fuel for electric vehicles containing fuel cells (FCEV), hydrogen as fuel for energy storage from renewable sources (P2G), hydrogen for industrial and domestic heating, and more.
About 99% of the hydrogen produced today comes from fossil fuel, and its production involves processes that emit carbon dioxide (CO2) into the atmosphere - a gas whose excess presence in the atmosphere accelerates global warming. The hydrogen is mainly produced by extracting it from natural gas (SMR) in a process that releases about 10 tons of CO2 for every ton of hydrogen and is therefore responsible for about 2% of the total CO2 emissions into the atmosphere that originate from human activity. This is the background for the urgent need for cleaner, more environmentally friendly alternatives for hydrogen production.
The main alternative available today to produce hydrogen cleanly and without CO2 emissions is water electrolysis. In this process, two electrodes, an anode and a cathode, are placed in water enriched with a base or acid that increases their electrical conductivity. In response to the transfer of an electric current between the electrodes, the water molecules (H2O) break down into their chemical elements and release hydrogen gas (H2) near the cathode and oxygen (O2) near the anode. The entire process takes place in an airtight chamber divided into two - in one part the hydrogen is collected and in the other the oxygen.
Producing hydrogen in clean ways, as opposed to producing it from natural gas in the SMR process, encounters a series of technological challenges. One of them is a significant energy loss; The energy efficiency of electrolysis processes today is only about 75%, which means: high consumption of electricity. Another difficulty is related to the membrane that divides the electrolysis cell into two; This membrane, required to collect the hydrogen on one side and the oxygen on the other, limits the pressure in the electrolysis cell to 10 to 30 atmospheres while in most applications a pressure of hundreds of atmospheres is required; For example, in electric vehicles containing fuel cells, compression of the hydrogen is required at a pressure of 700 atmospheres. Today, the pressure is increased using large and expensive compressors that complicate operation and increase the installation and maintenance costs of the system. In addition, the presence of the membrane complicates the assembly of the production facility and thus substantially increases its price. Beyond that, the membrane requires periodic maintenance and replacement.
The E-TAC water splitting technology has several significant advantages over electrolysis:
1. Complete chronological separation between the production of hydrogen and the production of oxygen - these two processes happen at different times. The consequences:
A. Eliminating the need for the separating membrane between the anode and the cathode in the electrolysis cell. This is a significant saving compared to electrolysis, since the membrane is expensive, complicates the production process and requires the use of distilled water and regular maintenance so that it does not clog.
B. A safe process, which avoids the risk of the explosive meeting between the oxygen and the hydrogen, a meeting that may occur in the normal electrolysis process in case the separating membrane is not completely sealed.
third. As mentioned, the current use of membranes limits the pressure in the hydrogen production process. The technology developed at the Technion makes the membrane redundant and thus enables compression of the hydrogen already at the production stage. In this way, some of the large costs associated with late compression of the hydrogen are also saved.
2. In the new process, the oxygen is created in a spontaneous chemical reaction between the charged anode and the water, without activating an electric current at that stage. This reaction saves the need for electricity in the oxygen generation stage and increases the efficiency of the process from about 75% in conventional methods to an unprecedented energy efficiency: 98.7%.
3. E-TAC technology is expected to reduce not only operating costs but also the cost of equipment. H2Pro estimates that the cost of equipment to produce hydrogen in the E-TAC process will be about half the cost of equipment based on existing technologies. The initial estimates indicate the possibility of producing hydrogen on an industrial scale at competitive production costs compared to production from natural gas in the SMR process, and this, as mentioned, without CO2 emissions into the atmosphere.
The developers of the technology, Prof. Gideon Gerder, Prof. Avner Rothschild and Dr. Chen Dotan, joined the founders of the Viber company and established the H2Pro company, which deals with the commercialization of the new technology. The company, which operates in the industrial park in Caesarea, received an exclusive license to commercialize the technology from 3T, the commercialization unit of the Technion Institute, and raised initial initial capital led by Hyundai. The company employs more than 20 employees, most of whom are Technion graduates.
The research was supported by the Nancy and Steven Grand Technion Energy Program (GTEP), the Ed Suttle grant, the Adelis Foundation, the Ministry of Energy and the European Commission (2020 Framework Program of the European Union).
For the full article in Nature Energy
For a video explaining the research, click here
3 תגובות
Outstanding development. The kind of research and development achievements that do not receive special titles, but their economic (and consequently - social, political and cultural -) importance in the medium term is very great.
As far as I understand from the article alone, distilled water is not required. A great idea indeed. Successfully
I think there is a slight inaccuracy.
I'm guessing the researchers used pure (distilled) water at the beginning of the process.
But there is no distilled water in nature, therefore even the preparation of the water has an energy cost that is interesting if it was taken into account.